Markono, a Singapore-based printing and logistics leader, transformed its manufacturing operations with Odoo ERP to overcome the challenges of disconnected systems. This case study reveals how a unified Odoo platform, featuring custom API integrations, enabled real-time data flow and automation across production, inventory, and finance, significantly improving efficiency and visibility for scalable growth.
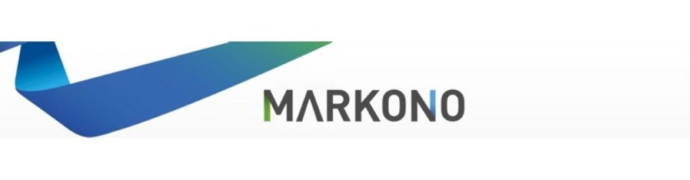
Company Name: Markono Group
Industry: Printing, Logistics, E-commerce
Location: Singapore (M-Cube, 18 Pioneer Crescent, Singapore 628567)
Company Size: Medium-scale company (100+ employees)
Current Scale: Providing digital and offset printing services, warehousing and fulfillment solutions, and e-commerce services for international publishers and Fortune 500 companies
Time of Implementation: 1 year (March 2020-April 2021)
Systems Implemented: Purchase, Sales, Inventory, Manufacturing, Accounting, Custom API Integrations, Custom Paper Conversion Module
A Legacy of Print Meets the Future of Fulfillment
Markono started its journey in 1967 as a traditional offset printing company. Today, it operates at the intersection of high-speed book printing, digital publishing, e-commerce logistics, and smart warehousing. The company prints books for major international publishers and provides fulfillment services for a fast-growing base of online retailers.
However, as its operations expanded across departments and verticals, Markono’s digital infrastructure struggled. Data silos, manual workflows, and system fragmentation limited visibility and introduced friction into critical processes, particularly impacting production planning, inventory control, and order fulfillment.
With rising order volumes and increasingly complex requirements, the leadership team knew it was time for a digital overhaul to address these operational challenges.
When Systems Don't Talk, Operations Stall!
Across five critical departments—Sales, Purchase, Inventory, Accounting, and IT—Markono's fragmented systems created mounting operational challenges. The manufacturing system lacked real-time visibility into sales and inventory data, leading to production inefficiencies. Their existing systems operated in isolation, including PrintAi for production and Infor for operations.
Manual workflows plagued every department: procurement teams struggled with purchase approvals, finance dealt with disconnected reporting, and e-commerce operations required constant manual intervention for order processing. Without system integration, each process bottleneck further limited the company's ability to scale.
Markono needed more than new software—they needed a unified technical foundation to bridge these operational gaps and enable seamless data flow across all systems and departments.
The Solution: One ERP, Endless Possibilities
Partnering with Portcities, Markono implemented Odoo ERP as its central integration platform. The solution bridged its PrintAi production system and Infor operations platform while enabling seamless data flow across all departments through custom API development.
Key modules implemented:
- Manufacturing: Machine-specific consumption tracking and overhead calculation, enabling precise production monitoring and cost control.
- Procurement: Advanced purchase workflows with blanket order capabilities and department-specific purchase request access.
- Inventory & Warehouse: Real-time inventory calculations and stock visibility across warehousing operations.
- Sales & E-commerce: Centralized order management with third-party platform integration.
- Accounting: Automated posting system with customized analytics rules for specialized financial reporting.
To address industry-specific requirements, Portcities developed custom solutions:
- API integration framework connecting PrintAi and Infor systems
- Specialized paper conversion module for optimizing material sizing and costs
- Automated customer invoicing system with email integration
- Custom analytics implementation for detailed operational reporting
Tangible Results Across the Board
With the new ERP in place, Markono saw significant performance improvements. Order processing became faster thanks to automated invoicing and synced e-commerce transactions. Inventory accuracy increased with real-time updates and tighter warehouse controls.
Production planning improved with machine-based consumption tracking, while accounting teams gained deeper visibility through automated entries and custom reporting. These improvements enhanced operational efficiency and created a foundation for scalable growth.
Today, Markono operates with a fully integrated ERP backbone that connects every aspect of the business. Automated procurement, synchronized sales and inventory, optimized production workflows, and enhanced financial analytics contribute to leaner, more agile operations.
With Odoo at the core and API connections to PrintAi and Infor, Markono can scale its services while maintaining control and quality.
Start Your ERP Journey With Portcities
If your manufacturing business is struggling with disconnected tools and manual processes, Markono’s success shows what’s possible with the right ERP system.
Let Portcities help you unify your operations and build a smarter foundation for growth.
Contact us to learn how we can support your growth with Odoo.